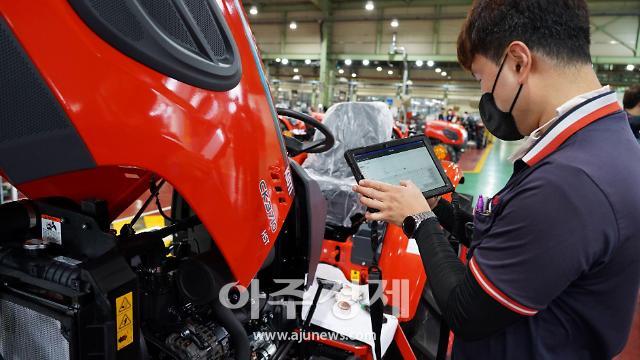
대동 대구공장의 농기계 생산 라인의 최종 검사장에서 작업자가 대동 MES(제조실행시스템)으로 트랙터 점검 사항을 확인하고 있다. [사진=대동]
대구상공회의소에서는 금융감독원 전자공시시스템과 신용평가사 등의 기업정보를 토대로 ‘2021년 매출액 기준 대구 100대 기업’을 파악한 결과, 2020년과 동일하게 2021년에도 대구은행, 에스엘이 1위와 2위를 차지했다. 3위는 2020년 기준 17위였던 엘앤에프가 14개 계단 상승하며 올라섰고, 4위에 대동, 5위에 대성에너지 순이었다.
4위를 차지한 대동은 2019년 매출액 기준 대구 100대 기업 중 7위에서 2020년에는 4위로 성장하고, 2021년에도 4위를 유지했다. 엘앤에프가 2020년에 17위에서 2021년에 14개 계단 상승하며 3위에 안착한 것은 2차전지 양극재 기업이 이제껏 10위권 밖에 머물렀지만, 전기차 1위 기업 테슬라에 니켈·코발트·망간·알루미늄(NCMA) 양극재를 공급하여 친환경 차 선호 흐름에 수혜를 보면서 높은 상승세를 보였다.
이에 대동은 미래농업 리딩기업으로 세계 수준의 생산 경쟁력 확보를 위해 대구공장의 스마트 팩토리 전환을 추진했다고 6월 30일 밝히며, 다가오는 2022년 매출액 기준 대구 100대 기업에서 괄목할 만한 성장을 기대하고 있다.
대동은 2020년 100년 역사의 ‘미래농업 리딩기업’의 비전을 선포하고 ‘비즈니스&프로세스 & 워크 이노베이션’을 위한 디지털 트랜스포메이션(Digital Transformation, 이하 DT)을 빠르게 추진 중이다. 이 중 하나로 2020년 말부터 글로벌 수준의 생산 경쟁력 구축을 위해 대동만의 ERP(전사적자원관리시스템), MES(제조실행시스템)을 재설계하고, 올해 상반기 대구공장의 스마트 팩토리 전환을 추진했다.
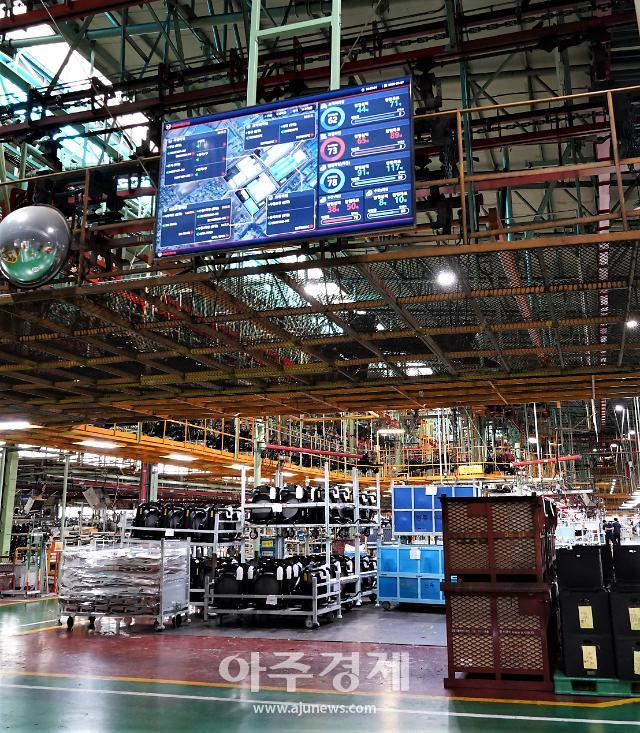
대동 MES(제조실행시스템)를 통해 디젤 엔진부터 완성형 농기계까지 모든 생산 제품의 실시간 생산 현황이 보인다. [사진=대동]
또한 스마트 팩토리 전환으로 대구공장은 디젤 엔진부터 완성형 농기계까지 모든 생산 제품의 실시간 생산 현황 모니터링이 가능하며 페이퍼리스(Paperless)를 지향해 관련 정보의 입력 및 확인 등을 키오스크, 태블릿 PC 등의 디지털 기기 등으로 진행한다. 스마트 팩토리 기본 시스템 구축으로 생산 과정에서 발생한 모든 빅데이터를 수집 중이며, 이를 기반으로 생산 설비부터 조립 품질의 이상 여부를 예측 제어하고 자율적으로 대응하는 고도화된 스마트 팩토리 시스템을 최종 구축할 계획이다.
이어 생산 주요 설비에는 센싱(온도,진동,속도)을 통해 실시간 작동 상태를 파악할 수 있으며, 이상 발생 시 작업자가 대동 MES에 증상을 입력하면 유관 부서로 전달돼 빠르게 고장 조치가 이루어진다. 센싱 데이터를 분석해 설비 고장, 안전사고 등의 문제 상황이 발생할 수 있는 이상 신호를 사전 포착해 선제 대응을 할 수 있어 생산 로스를 최소화해 생산 효율성을 높인다.
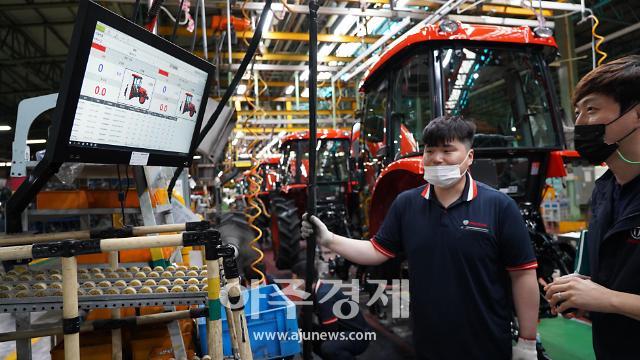
대동 대구공장의 농기계 생산 라인에서 작업자가 대동 MES(제조실행시스템)에서 자동 제공되는 트랙터 오일 주입량을 체크하고 있다. [사진=대동]
또 조립품 검사 과정에서 발견한 조립 불량을 MES에 입력해 검사와 정비 담당자에게 좀 더 상세하게 점검 사항을 전달, 철저한 출하 정비로 더 완벽한 제품을 고객에게 공급할 수 있다. 이 과정에서 발생한 빅데이터로 반복적으로 발생 되는 조립 불량에 대해서도 조립 방법이나 순서 변경 등의 선제 대응을 할 수 있어 시간 및 품질 로스를 한층 더 줄일 수 있다.
노재억 대동 공장장은 “대동은 대구공장을 중심으로 세계 70여 개국의 고객과 시장 상황에 맞는 제품을 ‘다품종 대량 생산’으로 공급하기 위한 생산의 유연성과 효율성의 극대화를 지속 추진하고 있다”라며, “스마트 팩토리 도입은 단순한 생산 자동화 시스템 구축을 넘어 설비, 제품, 품질, 물류, 재고 관리 등 업무의 모든 과정을 최적화함으로써 차별화된 기업 경쟁력을 확보하기 위한 것이다”라고 말했다.
©'5개국어 글로벌 경제신문' 아주경제. 무단전재·재배포 금지