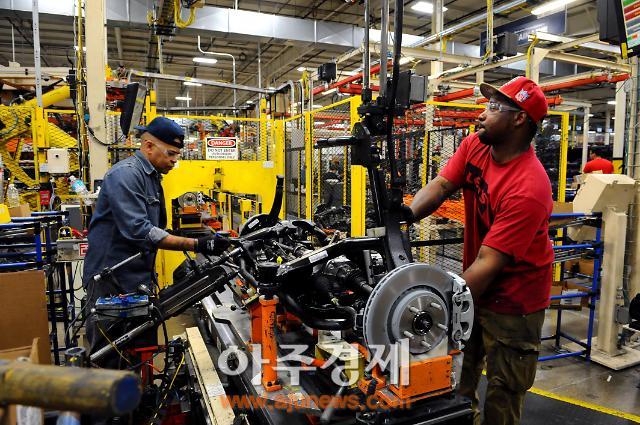
현대모비스 북미법인(MNA) 미시간 공장에서 크라이슬러 SUV 차종인 지프 그랜드 체로키와 닷지 듀랑고에 들어갈 프런트&리어 섀시 모듈을 작업자들이 조립하고 있다.[사진제공=현대모비스]
아주경제(디트로이트) 이소현 기자 = 지난 10일(현지시간) 미국 디트로이트 시내에서 남서쪽으로 약 5㎞ 떨어진 현대모비스 미시간공장.
이 곳은 현대모비스의 다른 글로벌 생산기지와 성격이 사뭇 다르다. 납품처가 현대·기아차가 아닌 미국 '빅3' 업체 중 하나인 크라이슬러다. 양질의 부품을 지속 공급하면서 지난해에는 크라이슬러의 최우수 협력업체로 선정되기도 했다.
이를 방증하듯 공장 내외부에는 ‘현대’의 흔적을 지운 채 ‘모비스’라는 브랜드를 강조한 모습이 역력했다.
김영석 현대모비스 북미법인(MNA) 생산팀 차장은 “올해로 11년째 크라이슬러에 모듈을 공급하고 있다"며 "납기 준수와 품질에 대한 신뢰가 바탕이 돼 크라이슬러와 지속적이고 발전적인 관계를 유지하고 있다”고 말했다.
이 곳에선 크라이슬러의 주력 스포츠유틸리티차량(SUV)인 지프 그랜드 체로키와 닷지 듀랑고에 들어가는 프런트·리어 섀시 모듈을 생산하고 있다. 지난 10년간 누적 공급량은 400만대에 달한다. 생산 첫해 10만대에 불과했던 생산량은 지난해 36만대까지 늘었다. 조업 형태도 1조 1교대 100여명에서 3조 2교대 478명으로 바뀌었다.
기존 현대모비스 공장이 ‘ㅡ’자 라인인 것과 달리 미시간 공장의 생산라인은 ‘ㅁ’ 모양을 띠고 있다. 지난 2009년 금융위기로 기존 크라이슬러 납품업체가 파산하면서 이를 현대모비스가 인수한 영향이다. 결국 현대모비스는 좁은 공간을 최대한 효율적으로 활용할 수 있는 ‘ㅁ’자 생산라인을 택했다.
떨어지는 생산성은 ‘액슬서브라인’을 통해 만회했다. 바닥에 깔린 자석을 따라 차량 1대 분량의 부품이 담긴 자재박스가 자동으로 움직여 작업자들에게 전달되는 무인공급시스템을 말한다. 생산성은 극대화할 수 있고 이종부품이 섞여 조립되지 않아 효율성을 높일 수 있다는게 특장점이다.
미시간 공장은 현대모비스 해외생산 공장 중 유일하게 ‘얼라이너’ 작업까지 진행하고 있다. ‘얼라이너’ 작업은 바퀴 정렬 상태를 측정하고 조정하는 것을 말한다. 보통 완성차 공장에서 진행하지만 크라이슬러의 요청에 의해 이곳에서 이뤄지고 있다.
미시간 공장은 지난해 말 수장이 바뀌면서 새로운 변화의 바람이 불고 있다. 일례로 매일 아침 7시30분 각 부서장들이 품질 실험실(Quality Lab)에 모여 품질회의를 진행한다. 때문에 잘못된 부분의 원인 분석과 함께 시정조치까지 ‘원스톱’으로 이뤄진다. 미시간공장 불량률이 100만대 중 500ppm으로 0.00001%에 불과한 이유다.
우경섭 현대모비스 북미법인장은 “업무, 생산, 품질, 문서 프로세스를 일원화해 기본에 충실한 표준화 작업에 힘쓰고 있다”며 “일하는 방식을 보다 경제적이고 효율적으로 만들어 품질 강화에 힘쓰겠다”고 강조했다.
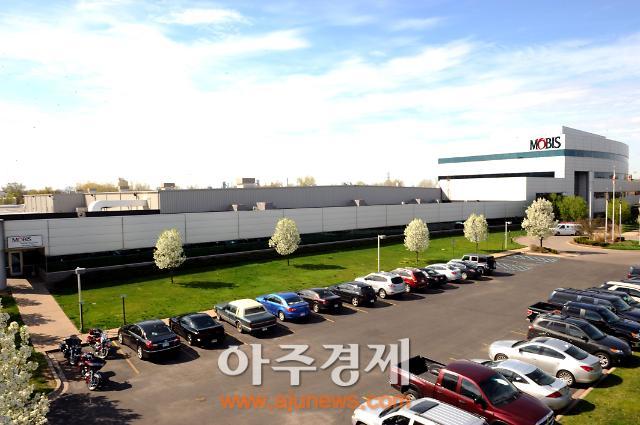
현대모비스 2만2770평 대지, 5840평 규모 미시간 공장 전경[사진제공=현대모비스]
©'5개국어 글로벌 경제신문' 아주경제. 무단전재·재배포 금지