한국항공우주산업(KAI)이 항공기 소재 국산화에 집중, 오는 2030년까지 사용하는 소재의 50%가량을 국산화한다는 목표를 세웠다.
18일 업계에 따르면 KAI는 올해 상반기 소재 국산화 TF를 꾸리고, 항공기 소재 연구개발(R&D)에 속도를 내고 있다. TF는 약 20명 규모로 소재를 담당하는 재료 공정팀 내에 설립됐다.
항공기 소재는 가벼우면서도 높은 강도와 내구성, 내열성을 가져야 해 각종 신소재가 다량으로 쓰인다. 하지만 대부분 수입에 의존하고 있다. 부품의 경우 국내에서 국산 기동헬기 '수리온', 한국형 전투기 'KF-21' 등을 개발하면서 국산화율이 높아지고 있지만, 소재 국산화율은 이제 막 걸음마를 뗀 수준이다.
KAI는 국내 항공용 소재 시장 규모의 상당 부분을 차지하고 있는 만큼 국산화에도 앞장서 국가 기술 경쟁력을 제고한다는 방침이다. 국내 항공용 소재 시장은 1조1200억원 규모다. 이 중 4000억원가량이 KAI에서 발생하는 수요다.
항공기 소재 기술은 최고 수준의 비밀 등급이라 단기간에 항공 선진국을 따라잡기는 어렵다. KAI는 공급처 간 컨소시엄을 구성해 개발 효율성을 높인다는 방침이다. 이를 위해 지난 2019년 10월 두산중공업, 효성 등 국내 기업과 재료연구원 등과 '항공소재개발연합'을 출범했고 지난해부터 본격 R&D를 진행 중이다. 현재 소재업체·시험기관·연구기관·대학 등의 22개 업체가 함께하고 있다.
실제 성과도 있었다. 수입되는 소재의 70%가량인 알루미늄의 경우, 국내 중소기업과 8개월간 개발한 끝에 국산화에 성공했다. KF-21 사업에서 알루미늄 압출재 33종 중 6종을 해당 재료 규격서 내 QPL(인정품목록, Qualified Products List)에 등재했다. 국산 소재가 항공용 재료규격서 QPL에 등재된 것은 처음이다.
또한 3D 프린팅 공정인 L-PBF(Laser Powder Bed Fusion) 공정도 재료·공정 규격서 등재 후 4종의 부품이 적용됐다. 3D 프린팅 파트에 적용되는 티타늄 분말 소재도 국산화 개발을 진행 중이다. 이 밖에도 본딩스트랩, 고강도 인장 및 전단 볼트와 너트, 도료 등에서도 국산화 개발을 추진하고 있다. 저압용 배관피팅의 경우 18종을 국산 부품으로 대체했다.
KAI는 소재 국산화를 통해 10% 이상의 원가절감, 30% 이상의 납기 단축 효과를 얻을 수 있을 것이란 기대다. 실제 지난해 구매로 이어진 20종의 경우 수입재 대비 60%의 절감 효과를 냈다. 또한 완성품을 수출할 때도 제3국 수출 금지 등의 각종 장애물이 사라져 수출 경쟁력을 높일 수 있다.
KAI는 소재 국산화를 군수기부터 시작해 민항기로 확대할 계획이다. 향후에는 도심항공모빌리티(UAM)와 개인용 비행체(PAV) 등 미래 모빌리티 분야에서도 국산 소재와 국내 생산을 통해 경쟁력을 확보할 계획이다. 앞서 KAI는 2029년까지 UAM 비행체 개발을 완료하겠다는 목표를 밝힌 바 있다.
KAI 관계자는 "소재 국산화는 기존에 획득한 기술을 바탕으로 한 장기적인 연구개발이 필요하다"며 "이미 개발한 기술에 대한 보호와 장기적인 연구개발, 육성정책 등도 중요하다"고 말했다.
18일 업계에 따르면 KAI는 올해 상반기 소재 국산화 TF를 꾸리고, 항공기 소재 연구개발(R&D)에 속도를 내고 있다. TF는 약 20명 규모로 소재를 담당하는 재료 공정팀 내에 설립됐다.
항공기 소재는 가벼우면서도 높은 강도와 내구성, 내열성을 가져야 해 각종 신소재가 다량으로 쓰인다. 하지만 대부분 수입에 의존하고 있다. 부품의 경우 국내에서 국산 기동헬기 '수리온', 한국형 전투기 'KF-21' 등을 개발하면서 국산화율이 높아지고 있지만, 소재 국산화율은 이제 막 걸음마를 뗀 수준이다.
KAI는 국내 항공용 소재 시장 규모의 상당 부분을 차지하고 있는 만큼 국산화에도 앞장서 국가 기술 경쟁력을 제고한다는 방침이다. 국내 항공용 소재 시장은 1조1200억원 규모다. 이 중 4000억원가량이 KAI에서 발생하는 수요다.
실제 성과도 있었다. 수입되는 소재의 70%가량인 알루미늄의 경우, 국내 중소기업과 8개월간 개발한 끝에 국산화에 성공했다. KF-21 사업에서 알루미늄 압출재 33종 중 6종을 해당 재료 규격서 내 QPL(인정품목록, Qualified Products List)에 등재했다. 국산 소재가 항공용 재료규격서 QPL에 등재된 것은 처음이다.
또한 3D 프린팅 공정인 L-PBF(Laser Powder Bed Fusion) 공정도 재료·공정 규격서 등재 후 4종의 부품이 적용됐다. 3D 프린팅 파트에 적용되는 티타늄 분말 소재도 국산화 개발을 진행 중이다. 이 밖에도 본딩스트랩, 고강도 인장 및 전단 볼트와 너트, 도료 등에서도 국산화 개발을 추진하고 있다. 저압용 배관피팅의 경우 18종을 국산 부품으로 대체했다.
KAI는 소재 국산화를 통해 10% 이상의 원가절감, 30% 이상의 납기 단축 효과를 얻을 수 있을 것이란 기대다. 실제 지난해 구매로 이어진 20종의 경우 수입재 대비 60%의 절감 효과를 냈다. 또한 완성품을 수출할 때도 제3국 수출 금지 등의 각종 장애물이 사라져 수출 경쟁력을 높일 수 있다.
KAI는 소재 국산화를 군수기부터 시작해 민항기로 확대할 계획이다. 향후에는 도심항공모빌리티(UAM)와 개인용 비행체(PAV) 등 미래 모빌리티 분야에서도 국산 소재와 국내 생산을 통해 경쟁력을 확보할 계획이다. 앞서 KAI는 2029년까지 UAM 비행체 개발을 완료하겠다는 목표를 밝힌 바 있다.
KAI 관계자는 "소재 국산화는 기존에 획득한 기술을 바탕으로 한 장기적인 연구개발이 필요하다"며 "이미 개발한 기술에 대한 보호와 장기적인 연구개발, 육성정책 등도 중요하다"고 말했다.
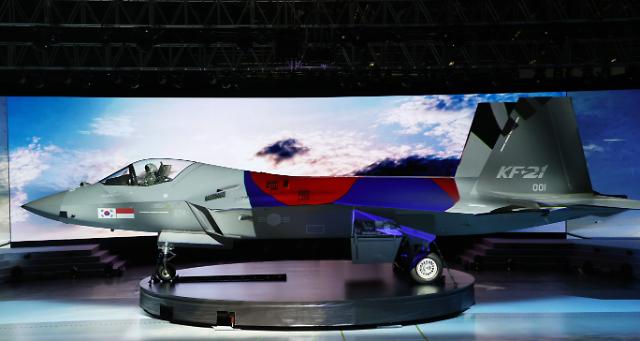
한국형전투기 보라매(KF-21) 시제기 [사진=연합뉴스]
©'5개국어 글로벌 경제신문' 아주경제. 무단전재·재배포 금지