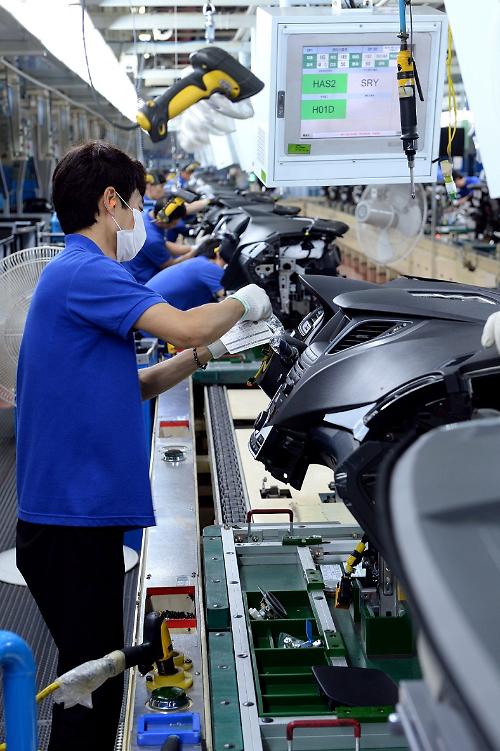
현대모비스 아산모듈공장에서 근로자들이 운전석모듈의 부품을 조립하고 있다.[사진=현대모비스]
아주경제(아산) 이소현 기자 = 현대모비스 아산모듈공장은 컨베이어밸트 돌아가는 소리와 제품을 조립하는 드릴소리로 가득한채 근로자들의 손길이 분주하게 움직이고 있었다.
아산모듈공장은 4만9300㎡(1만4940평)의 대지 위에 1만4289㎡(4330평)의 단층 건물로 첨단 시설을 갖춘 곳이다. 동양모듈, 이지테크, 현진모듈 등 총 5개의 협력사 400여명의 근로자들이 하루 2교대로 오전 6시30분부터 다음날 새벽 1시30분까지 작업을 진행한다.
지난 24일 12시께 충남 아산시 영인면에 있는 현대모비스 아산모듈공장. 공장입구에 있는 운전석 모듈 생산라인에 들어서자 2015년까지 글로벌 최고품질 달성을 독려하는 ‘GTQ(Global Top Quality)-2015 목표달성!! 내가 맡은 공정부터’라고 쓰여진 큼지막한 문구가 눈에 들어왔다.
파랑색 작업복에 목장갑을 낀 근로자들은 레고 블록을 만들듯 부품 조립에 여념이 없었고, 노란색 작업복과 조끼를 입은 근로자들은 부품 조립이 잘 됐는지 구석구석 살피고 있었다.
이영기 현대모비스 경인모듈생산실장(부장)은 “LF쏘나타가 지난 3월 출시된 이후 생산라인이 쉴 틈 없이 바쁘게 돌아가고 있다”고 말했다.
모듈은 일종의 ‘부품덩어리’다. 차량의 조립 공정에서 개별 부품을 하나씩 조립하지 않고 몇 개의 부품을 미리 조립해 덩어리째로 차체에 조립하는 방식이다. 이 공장의 연간 모듈 생산능력은 30만대다. 하루에 자동차 1000대분을 생산하며 모듈별로 계산하면 3000세트다. 한 시간에 66대, 54초에 한 대꼴로 만들어내는 셈이다.
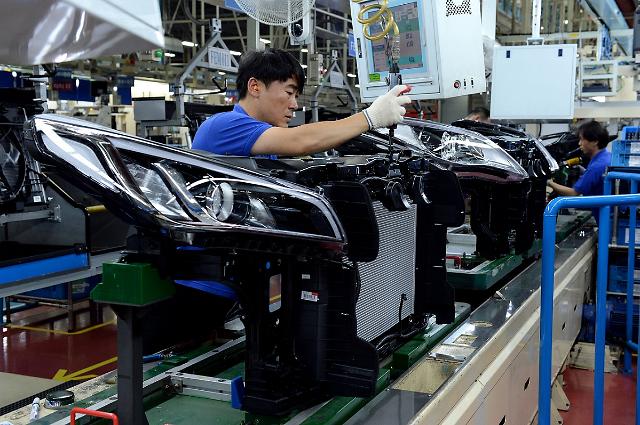
현대모비스 아산모듈공장은 샤시모듈(프론트/리어), 운전석모듈, 프론트엔트모듈 3대 핵심모듈을 양산한다.[사진=현대모비스]
아산모듈공장은 LF소나타를 비롯해 YF쏘나타와 HG그랜저의 3대 핵심모듈(샤시모듈‧운전석모듈‧프론트엔드모듈)을 같은 생산라인에서 동시에 양산하고 있다. 한쪽에서는 소나타의 모듈을, 옆에서는 그렌저의 모듈을 조립하고 있었다.
혹시나 부품이 섞이지 않을까 싶었지만 각 조립라인에는 바코드로 부품 식별이 가능했다. 또 모니터링이 가능한 화면에는 적절한 부품 조립시 초록색으로 ‘OK’사인이 표시됐으며 그렇지 않을 경우 빨간색으로 ‘NG’ 사인이 표시됐다. 불량 걱정 없는 체계적인 시스템이었다. 불량 건수는 10만대당 1~2건에 불과하다.
공장의 천장에 설치된 자동화 설비인 트롤리컨베이어 시스템은 쉬지 않고 계속 움직였다. 자동센서를 탑재한 무인운반대차도 ‘삐삐빅’ 요란한 소리를 내며 공장을 누볐다. 트롤리컨베이어는 주로 가벼운 부품을 근로자들에게 자동으로 전달하며 무인운반대차는 무거운 부품을 작업대로 옮기는 역할을 했다.
이렇게 만들어진 모듈은 12㎞ 떨어진 현대차 아산공장에 실시간으로 출하된다. 현대차로 차량 생산 주문이 들어오면 현대모비스도 모듈생산을 시작하는 직서열 생산시스템(JIS)덕분이다.
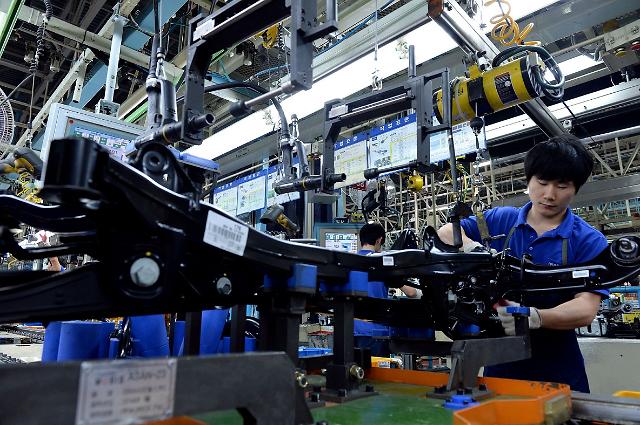
현대모비스 아산모듈공장은 이종방지(104항목), 기능검사(64항목), 체결보증(103개소), 장착성 등 4가지 품질 보증시스템을 운영하고 있다.[사진=현대모비스]
이 부장은 “재고관리에 있어서는 도요타의 적시 생산시스템(JIT)보다 현대 모비스의 JIS가 더 우수하다고 자부한다”며 자신감을 보였다.
JIT는 완성차 업체와 부품업체간 생산계획을 3~4시간 전에 공유하는 방식을 도입했지만 재고를 없애진 못했다. 반면 JIS는 주문이 들어오는 동시에 생산을 시작하기 때문에 재고가 발생하지 않고, 공간적 부담과 부대비용이 발생하지 않는 장점이 있다.
재고없는 실시간 납품을 위해 준비도 단단히 해뒀다. 예비도로는 물론, 단전되더라도 8초 이내 전기가 생산될 수 있도록 비상발전기가 마련돼 있다. 또 이 부장은 “시골길이라 요철이 많기 때문에 낙하방지를 위해 부품을 실은 트레일러에 단단한 고정장치를 장착한다”고 설명했다.
©'5개국어 글로벌 경제신문' 아주경제. 무단전재·재배포 금지